News & Resources
Featured
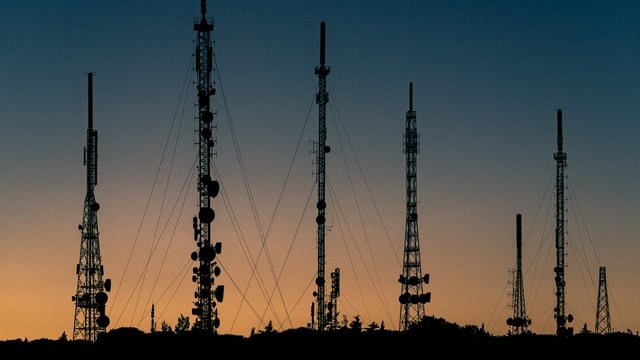
Protect Telecommunication Towers From Lightning Strikes
There is little argument that Lightning poses an enormous threat to telecommunication, radio and TV towers. These towers are constructed of steel and designed to be the highest
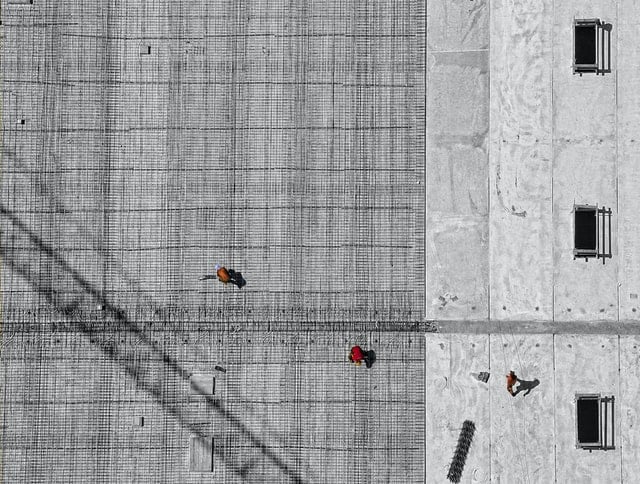
System 3000 Dynasphere Lightning Protection
There is little argument that Lightning poses an enormous threat to telecommunication, radio and TV towers. These towers are constructed of steel and designed to be the highest
Industry News, Product Updates & Resources
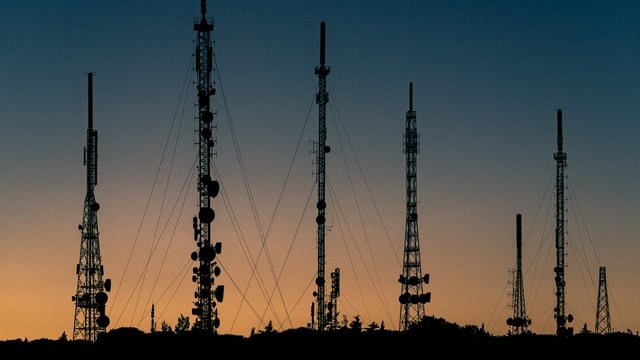
Protect Telecommunication Towers From Lightning Strikes
There is little argument that Lightning poses an enormous threat to telecommunication, radio and TV towers. These towers are constructed of steel and designed to be the highest structures in the surrounding area in order to supply communication with no interruptions. There is a higher probability of Lightning hitting the sharpest and tallest
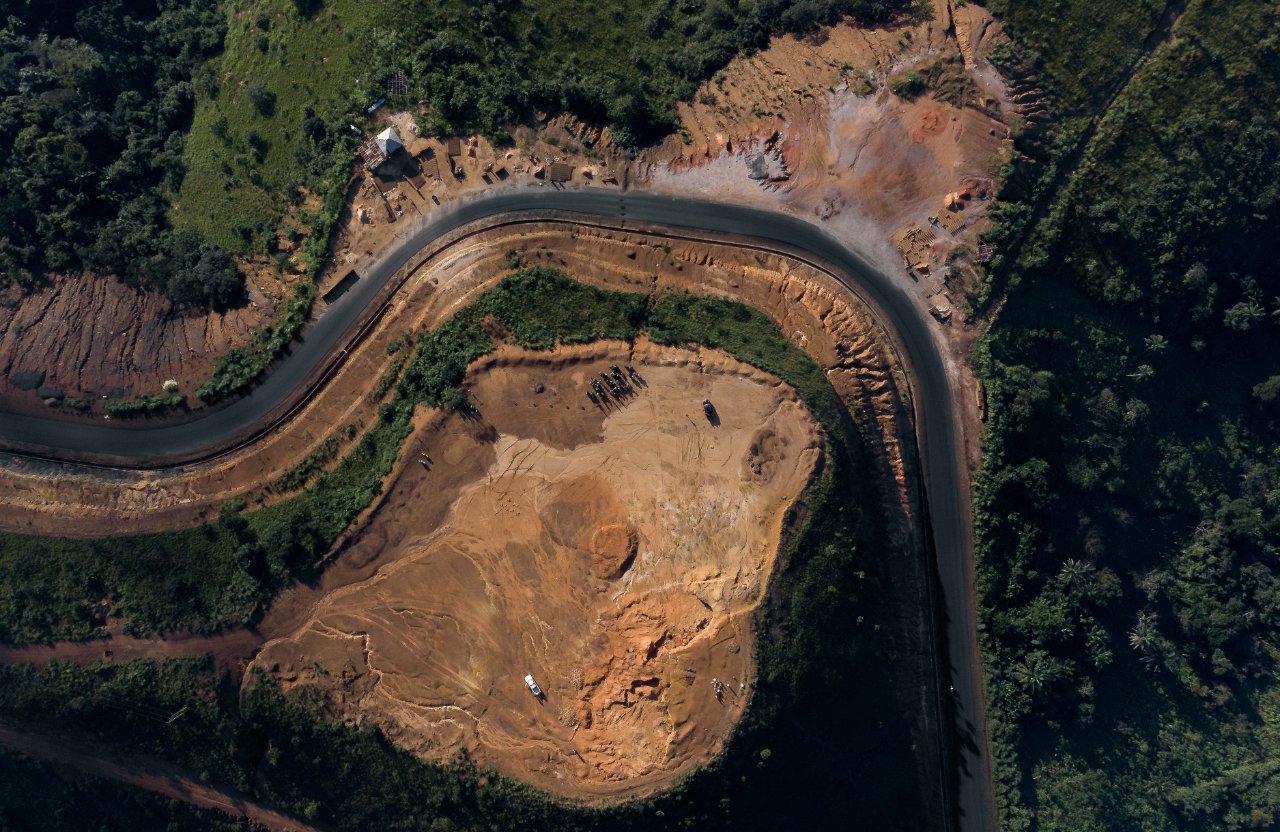
QUICKFILL – QF 25
nVent ERICO Quickfill is a no-mix ground-enhancing backfill that reduces resistance to ground and enables convenient installations. Quickfill is designed to minimize dust and eliminate mixing. It is the ideal material to use in areas of poor conductivity such as rocky ground, mountain tops, and sandy soil. Once installed, Quickfill
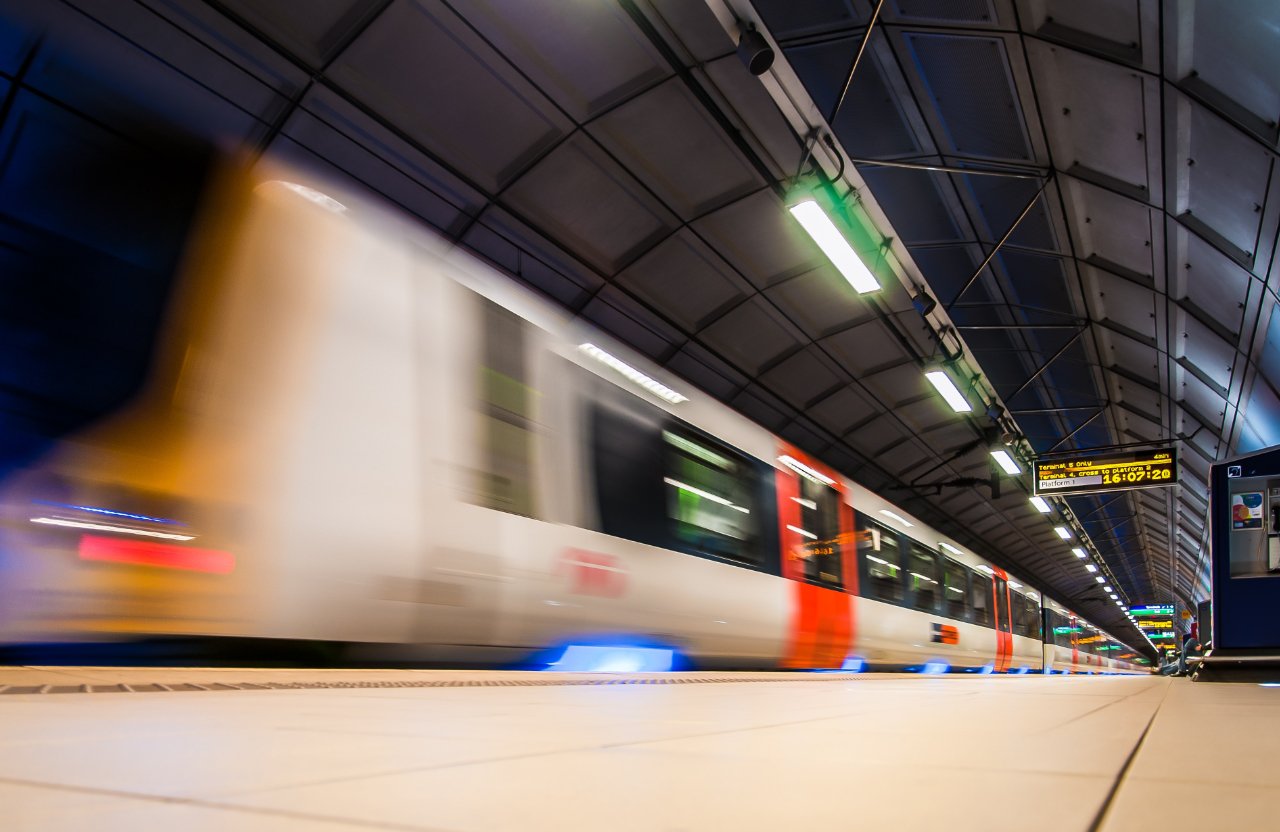
New Generation of ERICO RTB
nVent ERICO Introduces RTBN – The Next Generation Rail Data and Signal Protection. For many years railroads, have relied on nVent ERICO Rail Transient Barrier (RTB) products for protection against damaging voltage surges and transient events. Building on this legacy, nVent ERICO is pleased to introduce RTBN, the next generation in railway
Find A Product
Search our extensive range of products. We are the exclusive WA solutions provider for nVent Erico earthing, lightning and surge protection equipment.